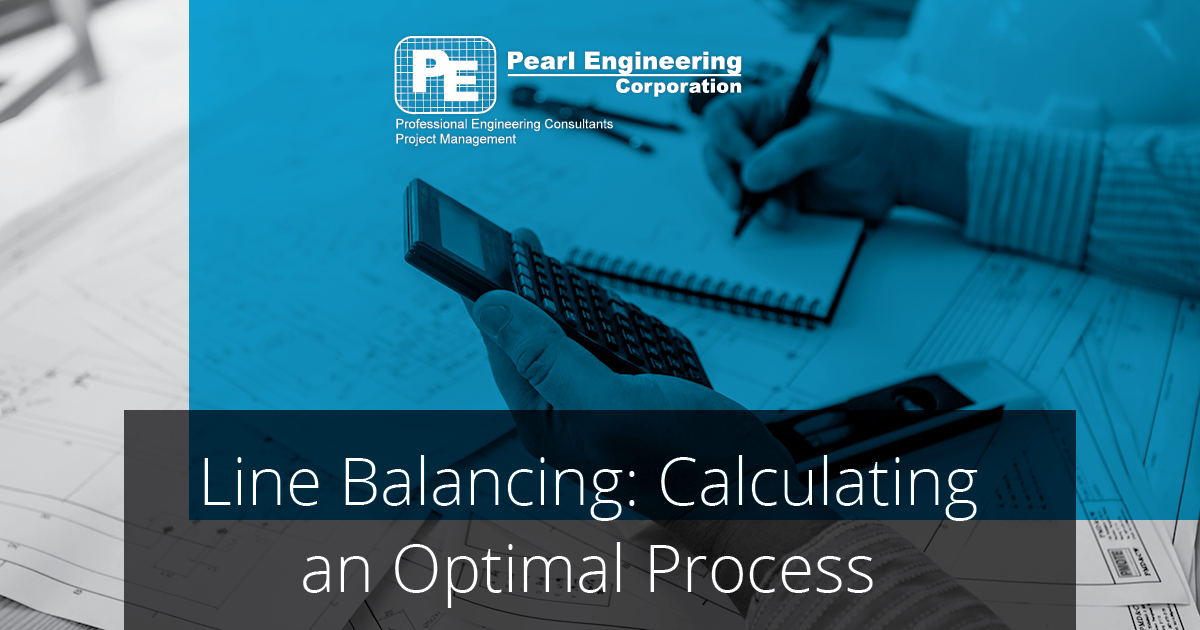
In a previous article, we covered the importance of improving process efficiency through process mapping, or a graphical representation and breakdown of how something gets done. Using a process map, you can identify potential bottlenecks and other breakdowns in the process preventing optimal performance.
While process mapping is an important method for improving process efficiency, it is far from the only tool organizations have at their disposal for taking a deep dive into their crucial processes and discovering areas of improvement. Another such method is line balancing.
When used alongside a thorough process map, line balancing’s mathematical approach to efficiency can help organizations more easily identify non-value added time, bottlenecks, and other breakdowns in their processes as well as providing direction on how to improve upon them.
What is Line Balancing?
Line balancing is a production strategy and efficiency optimization exercise that can be used to identify optimal production rates. Working backwards from there, this information can then be used to identify areas of improvement that will help get them closer to that optimal production rate.
This optimal production rate is known as Takt Time, the rate at which a product must be produced in order to meet customer demand. A production line that achieved balance between operator and machine time operates at a rate that meets their optimal Takt Time.
How do you calculate Takt Time?
Takt Time can be calculated using a simple mathematical equation: dividing the available working time per shift of staff and machines by the rate of customer demand per shift. It looks like this:
Takt Time = Available Working Time per shift / Rate of Customer Demand per Shift
A typical production line has roughly 480 minutes (or 8 hours) available per shift. However, a production line rarely utilizes every single hour and minute of the available time, as there are plenty of things that happen during the course of a day that are non-value added to the process, for example lunch breaks, changeovers, cleanup, and unplanned downtime. When calculating Takt Time, like process mapping, it is important to be as realistic and detailed as possible, meaning these need to be accounted for.
So, it can be safe to say that a typical line will likely have a total available time down to 360 minutes (or 6 hours) per shift. Of course, when calculating Takt Time for yourself, this may vary.
Calculating the other part of the equation, customer demand per shift, is far trickier. This factor is going to have to be a rough forecast based on supply and demand of your customers and the cycle time for purchases.
Finishing the calculation the number of units of your product that need to be produced in order to meet customer demands: the Takt Time.
Why is Line Balancing important?
This level of balance avoids two different, yet equally uncomfortable scenarios for a production line. The first, resulting from an abundance of working time vs low demand. This will result in a situation in which you have an abundance of inventory with no one to sell it to, losing money on inventory wasting away on the shelf.
The second, operating with low available working time vs a high demand, results in being unable to keep up with customer demands, causing a loss of business as frustrated customers will likely take their business to a competitor.
Operating with a balanced line means production is perfectly meeting the demand of your customers. In other words, as fast as you are able to move or sell your product, another one is ready to be sold.
Applying Line Balancing findings
Once Takt Time has been calculated, what should an organization do with the findings? Bottlenecks and preventable non-value added times are quicker and easier to identify once a cycle time’s Takt Time has been calculated as you can now compare how the processes should be completed versus how it needs to be completed.
One of the best places to start is by performing time studies. This exercise identifies the cycle time of each area in a process to strongly define the value added time versus the non-value added time or idle time. This part of the process is very similar to creating a process map, which is why process mapping and line balancing go so very closely together.
Using this analysis, an organization can more precisely notice which areas of the time study are exceeding the set Takt Time. If Takt Time is exceeded, that process has a bottle neck also known as a critical feature. From there, an organization must identify what changes can be made to address cycle time shortcomings.
For those facing high demand and low availability of labor, that could mean bringing in shifts over the weekend or investing in automation to account for the lack of manpower. Solutions may vary, but as Pearl Engineering Mechanical Engineering Associate Mike Evans explains, whatever the solution is needs to act as more than just a Band-Aid.
“Every process needs to be upgradable and adaptable for change,” he explained. “Doing so ‘future proofs’ your designs and processes, keeping them from immediately becoming obsolete.”
Ready to improve your processes?
Is an unbalanced line keeping your processes from maximizing their potential? The engineering team at Pearl Engineering believes in an efficient and methodical approach to every project we work with our clients on. Our team is experienced with process design, flows, and improvements. As a third-party consultant, we can offer an unbiased perspective and facilitation of your organization’s line balancing and process mapping projects.
Learn more about our experience with line balancing by contacting us or calling (715) 424-4008 today.